Q. Can I fix common waste disposer faults myself?
There are a few common faults that you may be able to resolve yourself, e.g. jamming, blockages, tripped overload switch.
Firstly, when fault finding, consider the type of waste disposer you have. Check out the video below to determine whether you have a high speed or standard machine. Once you know this, you can take the correct course of action for your particular machine.
QUICK BRAND REFERENCE:
High Speed Machines
Whirlaway
Applico
Waste King
Titan
Parmco
Smeg
Standard Machines
InSinkErator/Emerson
Kenmore
Robinhood/Scrapeater
Wastemaster
Typhoon
Q. Where is the reset switch on my waste disposer?
Most reset switches can be found on the bottom or the side of the machine, depending on the brand and model. See below for some common brands/models:
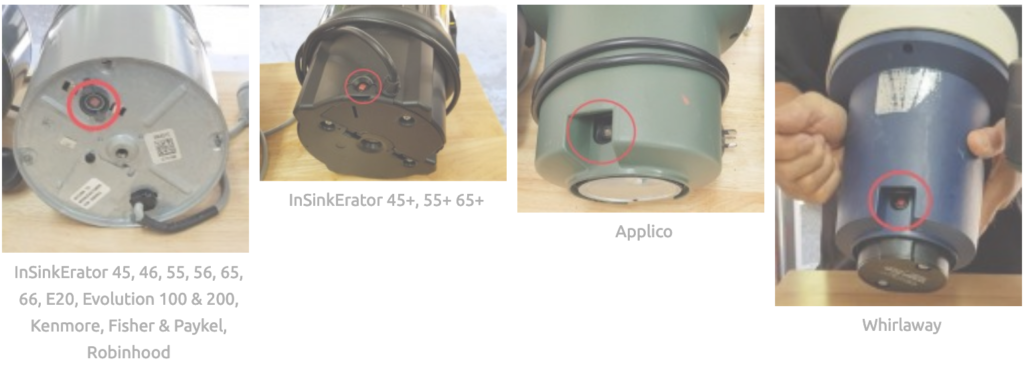
Q. Why doesn’t my waste disposer make any sound when turned on?
The overload has possibly tripped (situated under the base plate on some machines and on the side in a recess in the plastic housing on others). Disconnect the machine from the power outlet. Check there is nothing stuck in the machine and that the main plate, not the hammers, turns freely. Use the jam key to manually grind through any obstructions. Wait 5 minutes to allow to cool, then press the reset switch and try switching on the machine again.
Also check that the power plug is still connected under the sink. Sometimes this can be accidentally pulled out when items have been placed into the under sink cupboard. Confirm there is no power fault at the outlet by plugging in another appliance and testing.
If none of these resolve the issue, you will require a service visit.
Q. Why does my waste disposer just hum when I switch it on?
Most likely there is something stuck in the machine. Disconnect the machine from the power outlet and check for an obstruction. This can be done on standard speed machines (see Q1 video above for details) by inserting the jam key or a suitably sized Allen key in the centre of the base plate (underneath the machine). Check the main shredder plate is not floppy (indicating that it has detached from the motor shaft) and check for water leaks, stains or corrosion on the underside of the machine. The two latter faults indicate a motor shaft or seal failure which will require a replacement machine. If none of these resolve the issue, you will require a service visit.
Q. Why won’t my sink drain?
As your machine wears it will cut the scraps larger and in time you will possibly experience the odd blockage in the waste pipe. It may have one or both hammers jammed, unless it is a fixed hammer machine. Replacement or service may be required.
Q. Why has my waste disposer become noisy?
Food scraps can get lodged in the grinding teeth allowing the hammers (two opposing each other and fixed to the main plate inside the machine) to make contact with each revolution, or the hammers inside the machine have worn the fixing rivets. This allows the hammer to contact the outer grinding ring resulting in a clattering sound. Replacement or service may be required.
Q. What do I consider when purchasing a new waste disposer?
There are two distinct types of machine available. One derives torque from its high speed (a motor with brushes / armature and is physically light in weight) and the other is a split phase ac motor of approximately 1400 rpm which is considerably heavier.
When considering a new or replacement waste disposer thought should be given to the number of people the machine needs to service and the expected life of the machine. An incorrectly sized machine can result in premature failure with price generally reflecting quality.